How to Determine Your Packaging Line Layout
- CODI Manufacturing
- Aug 3, 2020
- 3 min read
Updated: Jul 14, 2021
When considering a canning line, each component should be scrutinized for quality and effective design. Choosing a robust system that will grow with your business will not only provide a strong return on investment but will also guarantee the quality of your beverage for distribution.
Select a Filler
Get our product in cans

Selecting the right beverage can filler is the first step in the equipment selection process for any canning system. The three most important aspects to consider when selecting a filler are: counter pressure fillers vs. open air fillers, cleanability of the machine, and mechanical engagement of seaming operations.
Counter pressure vs. open air fillers
Counter pressure technology offers the ability to easily package product within a wider temperature range and with higher carbonation levels than open air fillers. Counter pressure technology also reduces the amount of time the beverage is exposed to air effectively reducing final dissolved oxygen levels.
Cleanability of a machine is how well you can sanitize the equipment between canning runs. The problems of canning with a dirty machine can include distorted flavors and inconsistencies in packaged products. A filler must be able to endure high temperatures and caustic chemicals for extended periods. Choosing a filler of stainless steel construction that is wash down duty capable will ensure your product tastes the way you intended.
Mechanical seaming vs. Pneumatic seaming
Mechanical engagement of critical seaming operations ensures your cans are sealed consistently throughout every canning run. A seamer powered with pneumatics(compressed air) produces inconsistent seams due to drops in air pressure cutting the power supply for critical seaming operations.
Not all canners are created equal and are priced accordingly. Make sure to ask potential suppliers about the filling technology, cleanability, and seaming operations before making any decisions.
Determine if a Depalletizer is Required
Feed the filler

Depalletizing cans increases throughput and eliminates labor from the packaging floor. Adding a depalletizer to your canning line is a great way to free up employees for other essential tasks in the brewery. Start by looking at the standard design of the equipment. A good depalletizer should include the following features:
Advanced safety features such as light curtains that, when crossed, alert the user and shut down equipment. In the case of equipment failure, a counterbalanced system rather than a loop system will also prevent components from crashing down.
Limited moving parts above cans: keeps cans from collecting falling debris.
Intuitive user interface for controlling equipment operations and communicating with your filler.
VFD controlled motors: independently control functionality and speed of individual operations such as push speed and lower speed.
Slip sheet management: Slip sheets should be removed by lifting rather than sliding to reduce the possibility of tipping or damaging cans. A good depalletizer will also stack slip sheets off the floor for return to the supplier.
As the end user, you are responsible for keeping your employees safe within your facility. Choosing a supplier that engineers features like these into the design of the machine is important to good production and general workplace safety.
You mush also consider how far away the depalletizer will be from the filler. Does the manufacturer also design conveyance to work seamlessly with the depalletizer? Line integration problems can plague an owner for the life of the canning system. Solving these sort of issues up front will be beneficial in the long run.
Connecting Equipment with Conveyance
Going from Start to Finish
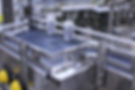
In any beverage filling application, the conveyance should meet standard design practices for food and beverage transport and the following features should be strongly considered when choosing a conveyance supplier.
Stainless steel components with wash down duty bearings and motors.
Stainless steel motor housings with wash down duty coatings and seals.
All fasteners are secured with lock washers or locking nuts.
Conveyor side rails are spaced away from the frame to allow for easy cleaning.
Washout flaps for easy access and cleaning of conveyance insides.
Post fill blower dry off system for drying cans before labeling and pack out.
Stainless steel drip pans with threaded half coupling for drain connections.
Manual or Automated Pack Out?
Distribute more Cans!
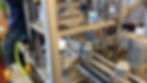
Combining cans into packs and cases for distribution can require significant labor. Manual pack out versus automated pack out depends highly on the output of the filler. There is not much need to use an automated packer for a canning system running less than 30 cans per minute. The same can be said for using manual pack-out labor when a canning system is running more than 100 cans per minute. It does not make sense to pay labor wages when a machine can do the work of 2 or 3 employees.
Once you choose the basic elements of your canning line, you can start thinking about additional equipment that will help differentiate your brand and increase efficiency. We offer labelers, date coders, twist rinses, warmers, pasteurizers, and various other equipment to solve all of your canning needs.